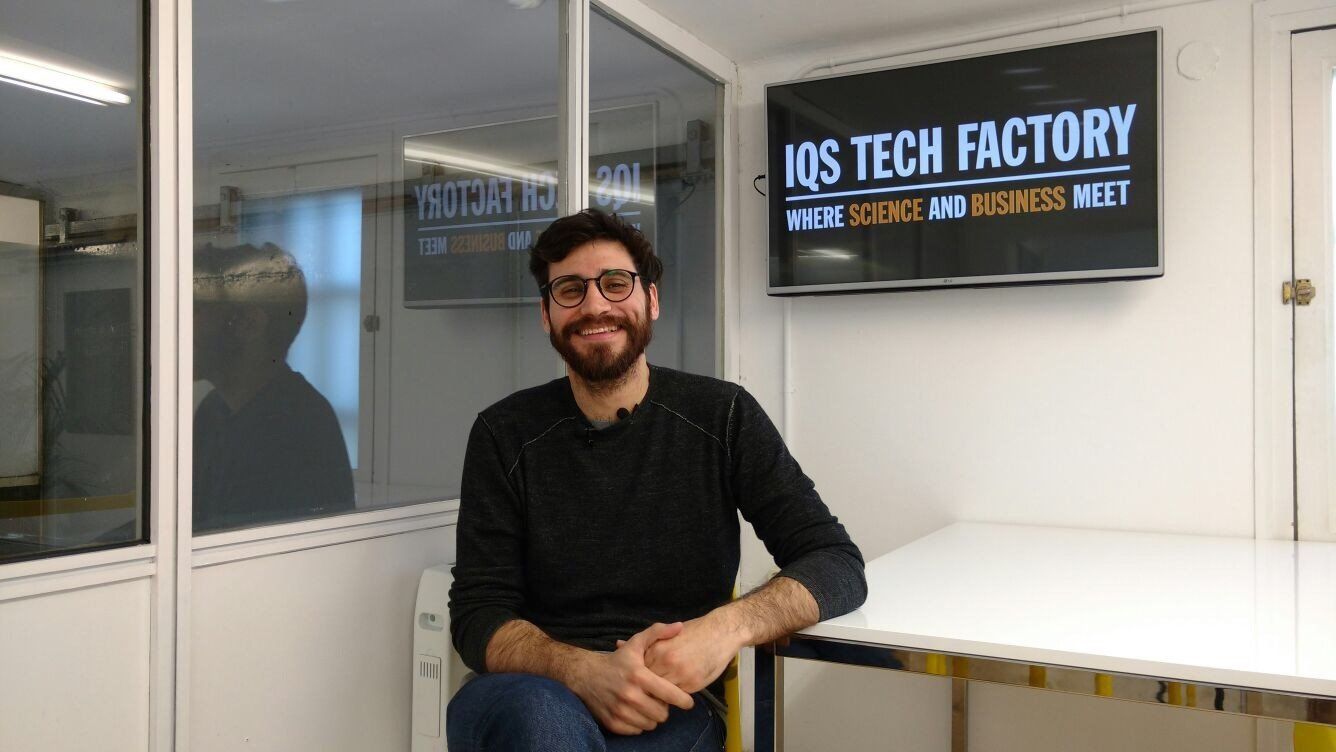
26
d'Abril
de
2017 - 10:11
Modelling and making a silicone trachea, one adapted to the patient and produced with 3D technology, is now a reality. This is what Tractivus does, a spin-off from the Chemical Institute of Sarrià and the IDIBELL-Institut d'Investigació Biomèdica de Bellvitge, that aims to solve the main complications in the medical sector caused by these implants.
The idea comes from the doctoral thesis of Joan Gilabert, the company's CEO, who in 2015 gave shape to his studies and set up the company. "We are currently working with prototypes and doing tests," he tells VIA Empresa, "but the aim is to come out on the market within two years at most." The team has four full-time engineers and a dozen partners helping to develop the project. Among them is IDIBELL, Bellvitge's Biomedical Research Institute.

Tractivus team. Ceded
An improved tracheal prosthesis
A conventional prosthesis is made of silicone and is cylindrical in shape; those by Tractivus, even though made of the same material, include antibacterial properties and a shape that better adapts to the patient. "The problem with interventions until now is that they do not adapt to the patient's anatomy and almost all of them are prone to infection. We reduce the danger of infection and make a personalised medical device with 3D technology," Gilabert points out.
At base, the device is no different from those already on the market, which will make its implementation quicker than if it had a new component or if there were an integral modification of the prosthesis. "We save a significant amount of regulation, which is a difficult thing to handle," says the CEO. He adds that they are talking to potential partners to transfer the base technology to other applications, such as catheters, to make new devices with an antibacterial covering and that are easier to adapt.

A 3D trachea madre by the startup. Ceded
At the moment, they are doing the first live tests, which will be crucial for the next phase of testing in Catalonia and Sao Paulo, where they are part of a medical research project.
A costly business to start
Since its inception, the spin-off has funded itself and relied on Neotec grants from the finance ministry. It is a quantity that Gilabert says is sufficient for the moment: "We have been able to develop prototypes and do some tests, but we will have to start thinking about starting an investment round."
If there is one thing about starting a business in the medical sphere, it is the cost of research and testing. "The materials, the manufacturing, the material for testing... all have high costs that cannot always be met," he says. It is a situation that pushes new companies to look for funding and technology in leading countries like the United States or Germany. "It is easier there to find resources and investors," insists Gilabert, "here we cannot raise 1,000,000 euros in a year just from family, fools and friends, but there you can."
However, he denies that looking abroad is to seek talent: "We have more than enough potential here; we have to believe in ourselves more. There are increasingly more State and Catalan subsidies, which help, but we need to attract money to develop the talent here." And this is where prizes like the Bioemprendedor XXI award come in, for which Tractivus was a finalist in 2014, because he says that it recognises the work done and helps to publicise innovative projects.
The idea comes from the doctoral thesis of Joan Gilabert, the company's CEO, who in 2015 gave shape to his studies and set up the company. "We are currently working with prototypes and doing tests," he tells VIA Empresa, "but the aim is to come out on the market within two years at most." The team has four full-time engineers and a dozen partners helping to develop the project. Among them is IDIBELL, Bellvitge's Biomedical Research Institute.
Tractivus team. Ceded
An improved tracheal prosthesis
A conventional prosthesis is made of silicone and is cylindrical in shape; those by Tractivus, even though made of the same material, include antibacterial properties and a shape that better adapts to the patient. "The problem with interventions until now is that they do not adapt to the patient's anatomy and almost all of them are prone to infection. We reduce the danger of infection and make a personalised medical device with 3D technology," Gilabert points out.
At base, the device is no different from those already on the market, which will make its implementation quicker than if it had a new component or if there were an integral modification of the prosthesis. "We save a significant amount of regulation, which is a difficult thing to handle," says the CEO. He adds that they are talking to potential partners to transfer the base technology to other applications, such as catheters, to make new devices with an antibacterial covering and that are easier to adapt.
A 3D trachea madre by the startup. Ceded
At the moment, they are doing the first live tests, which will be crucial for the next phase of testing in Catalonia and Sao Paulo, where they are part of a medical research project.
A costly business to start
Since its inception, the spin-off has funded itself and relied on Neotec grants from the finance ministry. It is a quantity that Gilabert says is sufficient for the moment: "We have been able to develop prototypes and do some tests, but we will have to start thinking about starting an investment round."
If there is one thing about starting a business in the medical sphere, it is the cost of research and testing. "The materials, the manufacturing, the material for testing... all have high costs that cannot always be met," he says. It is a situation that pushes new companies to look for funding and technology in leading countries like the United States or Germany. "It is easier there to find resources and investors," insists Gilabert, "here we cannot raise 1,000,000 euros in a year just from family, fools and friends, but there you can."
However, he denies that looking abroad is to seek talent: "We have more than enough potential here; we have to believe in ourselves more. There are increasingly more State and Catalan subsidies, which help, but we need to attract money to develop the talent here." And this is where prizes like the Bioemprendedor XXI award come in, for which Tractivus was a finalist in 2014, because he says that it recognises the work done and helps to publicise innovative projects.